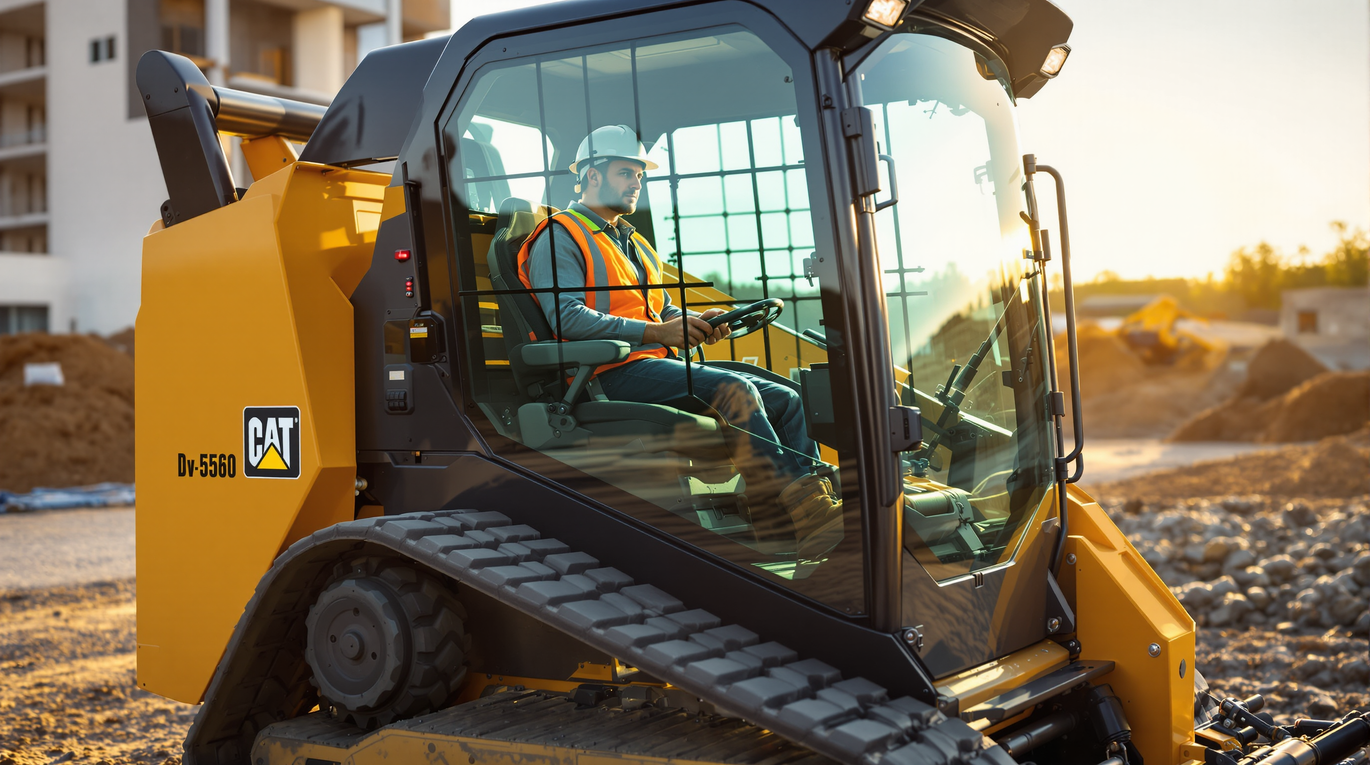
Productivity rises when skid loader operators feel comfortable at work. The data backs this up. Operators look at six significant features to evaluate their equipment effectively: visibility, comfort, simplicity, attachments, power, and capacity. These elements affect their performance and overall well-being daily.
Operator fatigue hits employers' wallets hard, costing $1,200 to $3,100 per employee each year through missed workdays and healthcare costs. Equipment manufacturers now design modern machines with electronic-hydraulic controls. These controls need minimal resistance and make operations easier while reducing physical strain.
This piece explains the importance of ergonomics for skid loader operators. You'll learn about cutting-edge equipment features and what makes an operator-friendly work environment. The proper ergonomics can reshape your work experience completely, whether you operate skid loaders now or plan to start this career.
Physical Demands of Skid Loader Operation
Skid loader operators face physical challenges that go way beyond the reach and influence of basic machine operation. Research reveals these operators experience the most important whole-body vibration exposure. The vibration frequencies range from 2 to 100 Hz during normal operation.
Common operator movements
A skid loader operator's daily routine requires constant physical activity. These operators repeatedly perform tough movements:
- Neck and trunk twisting to see properly
- Stretching to reach controls
- Holding fixed positions for long periods
- Getting in and out of the cab
- Regular use of foot and hand controls
Research shows high rates of musculoskeletal problems among operators, especially when you have lower back (53%), mid-back (42%), and neck, shoulders, and buttocks (37%).
Impact on body over time
Operating skid loaders for years puts heavy strain on the body. Research shows construction equipment operators develop higher breathing and heart rates. They also experience problems with position awareness, balance, and visual performance.
The mix of whole-body vibration and awkward positions creates serious health risks at work. The largest longitudinal study of heavy equipment operators showed that 72 million males and 1.8 million females in the United Kingdom deal with whole-body vibration.
Older operators feel these physical effects more strongly. Research proves experienced senior workers face extra challenges as their bodies become less flexible and take longer to heal from injuries. Their joints become less tolerant over time, which affects their hand and wrist strength.
The construction industry reports a concerning 30% incident rate for musculoskeletal disorders. This means about 600,000 workers in construction suffer from these conditions. These disorders cost between $45 to $54 billion yearly in the United States.
Key Ergonomic Features Modern Operators Need
Modern skid loader designs put operator comfort first with advanced ergonomic features that tackle common workplace challenges. These new features help reduce physical strain and boost productivity.
Adjustable seating systems
Skid loader seats now come with sophisticated suspension systems that cut down whole-body vibration. Premium models come with air-ride seats that offer full adjustability for recline, slide, weight, and four-way armrests. These seats include:
- Breathable cloth materials with operator-controlled heating
- Lumbar support adjustment that prevents lower back pain
- Shock absorption systems
- Asymmetrical backrest design for better rear visibility
The latest seat designs fit operators of all sizes, with weight adjustments up to 375 pounds.
Control placement
Control systems have improved by a lot to cut down operator fatigue. Electronic-hydraulic controls need much less effort compared to traditional mechanical linkages. Operators now make up to 75% fewer hand motions inside the cab.
Single-sided lap bars give operators more comfort by creating extra space around their waist. The easy-to-use switch placement and adjustable joystick controls make repetitive actions easier throughout the workday.
Visibility improvements
New cab designs offer much better visibility. Modern skid loaders now have 22% more glass area and 26% additional foot space. The cab posts have moved back more than 3 inches to create a wider view through exclusive three-section sliding windows.
Floor-to-ceiling visibility includes all-clear sides and frameless doors that give almost 360-degree views while keeping operators safe. Operators don't need to change position as often to see clearly.
Climate control options
Climate control systems now adjust temperature automatically. The cab's one-piece sealed and pressurized design keeps dust and dirt out while blocking engine and hydraulic noise.
Multiple vents are placed strategically for the best comfort in extreme temperatures. Special front door seals increase cab pressurization and keep heated or air-conditioned air inside. This better environment helps operators stay focused on their work without getting distracted by outside conditions.
How Better Ergonomics Affects Daily Work
Research shows that better ergonomics in skid loader operations helps both operators and employers. Studies on ergonomic changes reveal big improvements in workplace safety and efficiency.
Reduced operator fatigue
Better ergonomics affects how long operators can work comfortably. Studies reveal that operators who use machines with advanced ergonomic features have 32.5% lower upper extremity pain. These improvements help operators stay alert and precise during their shifts.
Operators who work with ergonomically designed equipment report much lower back pain. The cost of adding ergonomic features might seem high at first, but the long-term benefits are worth the investment.
Increased productivity
Research data clearly shows the link between operator's comfort and productivity. Operators in ergonomically improved environments show better results in key areas:
- 66% reduction in workplace incidents
- 81% decrease in cost per employee
- 30% reduction in cost per claim
These improvements create real business benefits. Companies that invest in ergonomic equipment see better operator retention and spend less on training new workers.
The financial benefit is huge, as studies show ergonomic improvements can save $45-54 billion annually in workplace injury costs. Skid loader operators who work with well-designed equipment show higher precision and efficiency in their daily work.
The benefits go beyond immediate productivity gains. Operators using machines with advanced ergonomic features show improved performance when tasks need precise control and longer operation times. These improvements stand out when operators need to make repeated movements or work for extended periods.
Better workplace efficiency comes from features like customizable controls and improved visibility systems. Studies show that operators finish tasks faster with ergonomic improvements because they feel less physical strain and stay focused longer during their shifts.
Current Skid Loader Operator Challenges
Skid loader operators deal with unique challenges that go beyond simple machine control. These challenges affect both safety and productivity in work environments of all types.
Long work hours
Long hours put heavy physical and mental strain on skid loader operators. Studies show operators who work long shifts have trouble with motor skills and speech because they get tired. Many companies try different shift patterns to boost productivity, but finding the right balance is tough.
A strategy that works well uses four-night and five-day shifts, and night crews finish on Thursday evening. This schedule lets operators get enough rest between shifts to stay alert. In spite of that, studies show extended shifts can make operators tired and less effective.
Varied terrain conditions
Different terrains create special challenges for skid loader operators. Uneven ground affects machine stability and how well operators can work. The biggest problems include:
- Poor traction on concrete floors and ramps
- Higher chances of tipping on steep slopes
- Hard to stay stable with heavy loads
- Tough to move through rough and uneven ground
Studies show that working on steep slopes or shaky ground can cause serious accidents when machines become unstable. Operators must also change how they work based on ground conditions to get the best results.
Weather impacts
Weather can make operating skid loaders really challenging. Studies show tire pressure drops by 1 psi for every 10°F temperature decrease. This changes how stable and effective machines are in cold weather.
Cold weather brings several key challenges:
- Higher risk of getting dehydrated in cold weather
- Hard to see through foggy or icy windows
- More likely to slip and fall on icy surfaces
- Problems keeping proper tire pressure
Operators working in very cold weather face health risks beyond normal challenges. Winter dehydration becomes a real issue as cold pushes body fluids toward the core, making you pee more and possibly get dehydrated.
Bad weather also affects how the equipment works. Frozen metal can cause cold burns, and wet skin touching frozen surfaces creates safety risks. Operators also struggle with poor visibility from snow and ice that can hide dangerous ground hazards.
Finding Ergonomic-Friendly Skid Loader Jobs
A safe, ergonomic workplace starts with knowing what to look for in job opportunities. We found that proper workplace ergonomics helps prevent musculoskeletal disorders affecting over 600,000 workers in the construction industry each year.
What to look for in job listings
Smart job hunters should check job descriptions carefully for signs of ergonomic awareness. Job listings that mention modern features like adjustable seating systems and electronic-hydraulic controls show the company cares about operator comfort.
Companies that mention regular equipment maintenance schedules and operator training programs usually take workplace safety seriously. You'll notice good employers highlight ergonomic features in their equipment descriptions, such as pressurized cabs or dual-level suspension systems.
The best positions offer rotation through different tasks or scheduled breaks that reduce physical strain during long operations. Job listings that describe complete training programs often come from employers who value proper ergonomic practices.
Questions to ask employers
Your interview is the perfect time to ask about workplace ergonomics and safety measures. Here's what you should find out:
- Equipment maintenance schedules and upgrade policies
- Operator training programs and safety protocols
- Work rotation policies and break schedules
- Availability of ergonomic assessment tools
- Incident reporting procedures and response protocols
Good employers follow OSHA guidelines and should have clear protocols to identify and fix ergonomic hazards. Ask them how they assess workplace conditions and make improvements.
The company should support early reporting of injuries and have clear protocols for ergonomic concerns. Make sure you understand how they handle workplace modifications when operators report discomfort.
Try out the equipment before taking the job. This helps you check if the machine's ergonomic features suit your needs. Look around for proper safety measures like cushioned mats in loading areas or non-slip materials on footrests.
The employer's commitment to periodic reviews of facility and workstation designs matters a lot. Good companies regularly assess their facilities and welcome worker feedback about ergonomic improvements.
Smart candidates ask about investments in modern equipment features like air-ride seats with full adjustability and improved visibility systems that minimize operator strain. The best organizations proudly showcase their advanced technologies that boost operator comfort and reduce fatigue.
Conclusion
Good ergonomics changes skid loader operation from a physically demanding job into a sustainable career path. Research shows that operators who use ergonomically designed equipment experience 32.5% less upper body pain and show substantially higher productivity levels.
Equipment manufacturers have created innovative features to meet these needs. Advanced suspension seats, electronic controls, and improved visibility systems now come standard. These improvements reduce operator fatigue and deliver substantial cost savings by decreasing workplace injuries and improving efficiency.
The success of a skid loader operator depends on finding employers who make ergonomic equipment and operator well-being their priority. Smart operators should assess potential workplaces and look for companies that invest in modern machinery with clear safety protocols.
The future of skid loader operation depends on ergonomic excellence. Companies that embrace these improvements protect their workers and gain measurable advantages through increased productivity and lower operational costs. Smart choices about equipment and workplace conditions today will give operators a healthier, more productive tomorrow in this industry.